An Introduction to Arc Flash

Heightened awareness of electrical arc flash hazards has created a demand for safer workplaces. This article presents a brief introduction to arc flash, including an explanation of what arc flash is, a list of common causes, and a look at some of the standards related to arc flash.
Only One Piece...

Although the focus of this article is arc flash, this is only one piece of electrical safety. Working on or near energized electrical equipment has long been recognized as a serious workplace hazard, exposing personnel to electric shock, electrocution, burns, fires, and flashover events. Creating a safe workplace presents an ongoing challenge, and you may find the standards which govern electrical safety practices to be confusing. In addition to arc flash risk assessments, DMG offers comprehensive electrical safety services to help address the hazards present in your facility, including:
Electrical Safety Audits
Electrical Safety Training
Arc Flash Risk Assessment
PPE Selection and Sizing
Lockout/Tagout Audits
What is arc flash?

OSHA Definition
OSHA defines arc flash as a phenomenon where a flashover of electric current leaves its intended path and travels through the air from one conductor to another, or to ground.
The Physics

As we remember from our Physics courses, when an electrical potential or an applied voltage is present, the available electrical charge or current seeks to complete the circuit and flow back to the source. When this current finds an alternate path—flowing through ionized air—an arc flash results.
Excessive Heat
When a large amount of energy is available (e.g. a utility supplied current), a large amount of heat can be generated. Arcing temperatures in facilities can reach 35,000°F, which is three times hotter than the sun.
Flashover
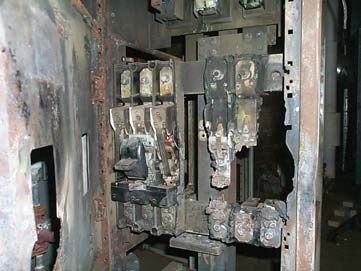
These excessive temperatures can cause the air and metal near the path of the arc to superheat, expand, and explode.
Further Effects
Additional side effects can include results similar to an explosively formed projectile (EFP). Droplets of molten metal and shrapnel produced by the arc can be spread over a large area. Blast pressure waves can throw workers across rooms and knock them from ladders.
What are some common causes of arc flash incidents?

Equipment Failure
When insulation or isolation between energized conductors is no longer sufficient to withstand the applied voltage, an arcing fault can occur.

Atmosphere
The presence of dust, vapor, corrosion, dripping water, or other conductive imperfections in the air can also lead to an arcing fault.
Human Interference

Human actions cause the overwhelming majority of arc flash incidents. Many electrical work activities require personnel to be in close proximity to energized conductors. For example, common causes of arcing faults include voltage testing, fault finding, commissioning, circuit breaker racking failure, misplacement of test probes, dropping tools on live conductors, improperly utilizing equipment, improper work procedures, etc.
What regulations apply to Arc Flash?

History
Historically, the National Electric Code (NEC) and other safety codes were primarily concerned with protection from fire, electrocution, and shock hazard—arc flash hazards were not addressed. Increased awareness has led other codes, standards and insurance providers to address arc flash hazards.
Timeline
1970—OSHA is developed to protect workers
1976—NFPA 70E was developed specifically to address electrical safety for employers, employees, and OSHA.
1982—Ralph Lee develops maximum power theorem, a theoretical method to predict arc energy
1995—NFPA 70E first references arc flash
2000—NFPA 70E introduces PPE requirements and hazard risk tables
2002—IEEE 1584 is published and includes a set of incident energy calculations which are empirically derived equations based on extensive laboratory test data
2002—NEC first requires arc flash warning labels
2007—NESC is updated to require arc flash for electric utilities
2014—OSHA language is updated to require arc flash risk assessments
2015—NFPA 70E additional labeling requirements
Codes and Standards
OSHA 29 CFR 1910 requires employers to perform a PPE hazard assessment to determine necessary PPE, provide required PPE, and implement safe work practices.
NFPA 70E-2015 requires an arc flash risk assessment be performed.
IEEE 1584 provides a guide for performing arc flash hazard calculations.
Solutions
Arc Flash Risk Assessment and Labeling
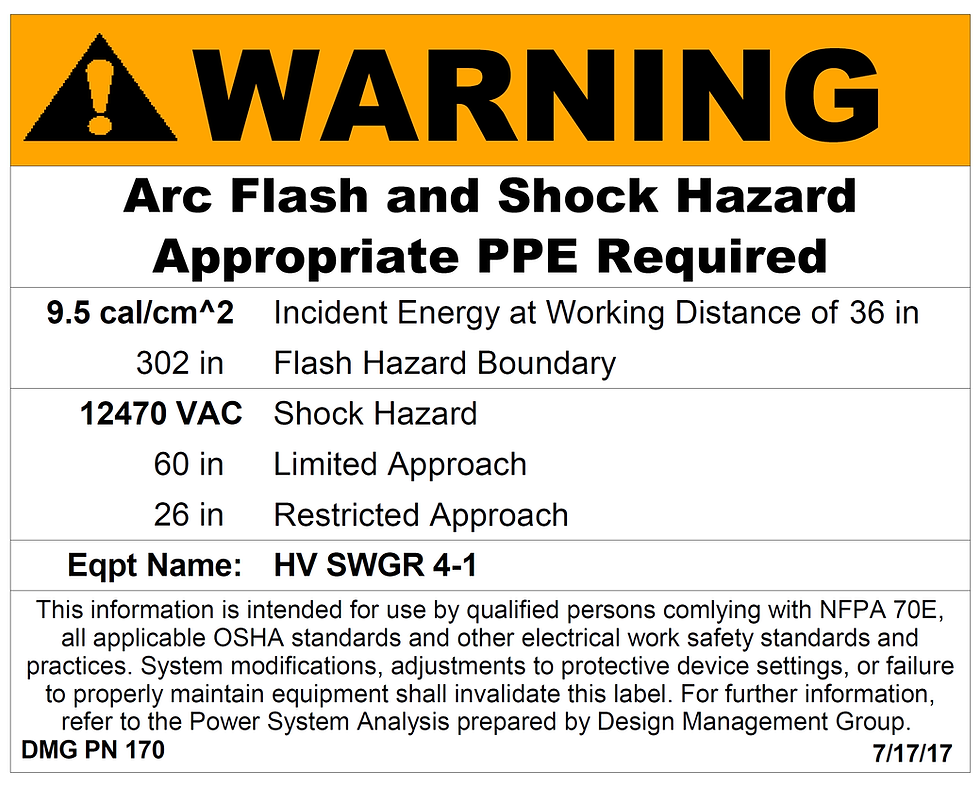
DMG can help to institute a labeling practice per NFPA 70E—the industry preferred method for complying with OSHA 29 CFR 1910 and increasing arc flash safety. Based on an arc flash risk assessment prepared by DMG, warning labels meeting NFPA 70E standards are provided with information to warn qualified personnel of the available incident energy, shock hazard, etc.
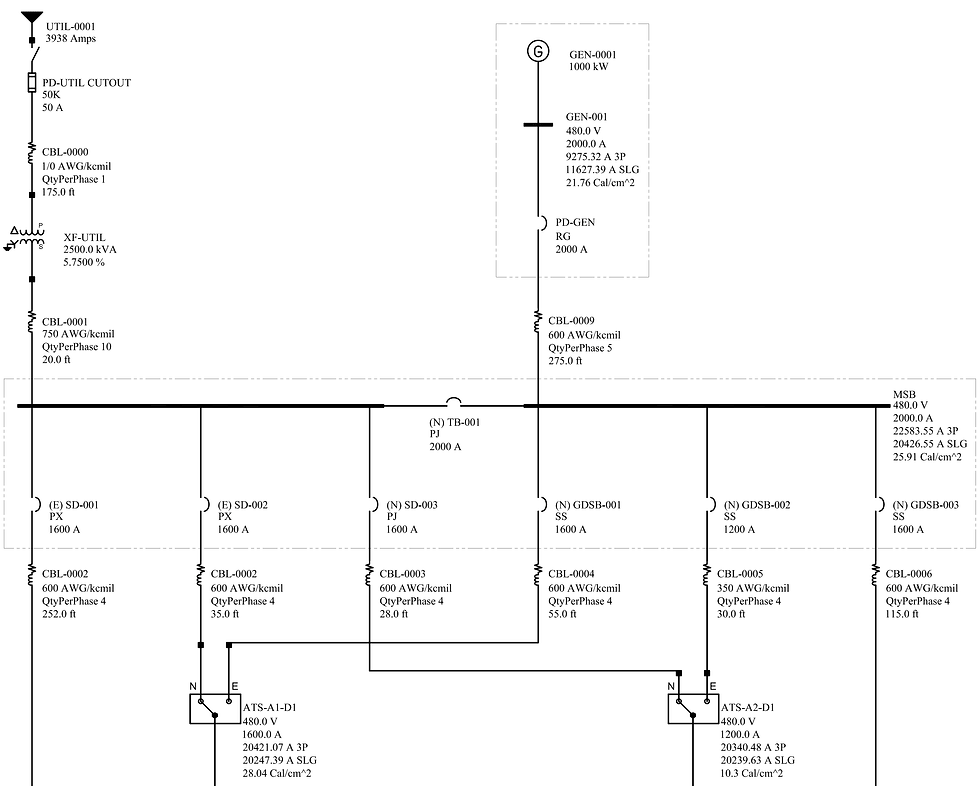
In order to perform an arc flash risk assessment, registered electricians (the facility’s or DMG’s team) perform a detailed survey of the system. DMG's Power Systems Engineering Team uses the collected data to build a model of the system in a power analysis software suite. The model is used to develop an analysis of the system and corresponding equipment per the IEEE 1584 and NFPA 70E guidelines.

DMG's complete code compliant solutions are offered as a deliverable to meet new construction project specifications or as a service in existing facilities. For a more technical discussion on arc flash, electrical safety, or related topics such as overcurrent protective device coordination, feel free to reach out to us today!
Access to the relevant IEEE, NFPA 70E, and OSHA standards is available through the links below:
If you need help with an arc flash risk assessment or any other electrical engineering service, contact us today!
Building Systems, Safer...
with
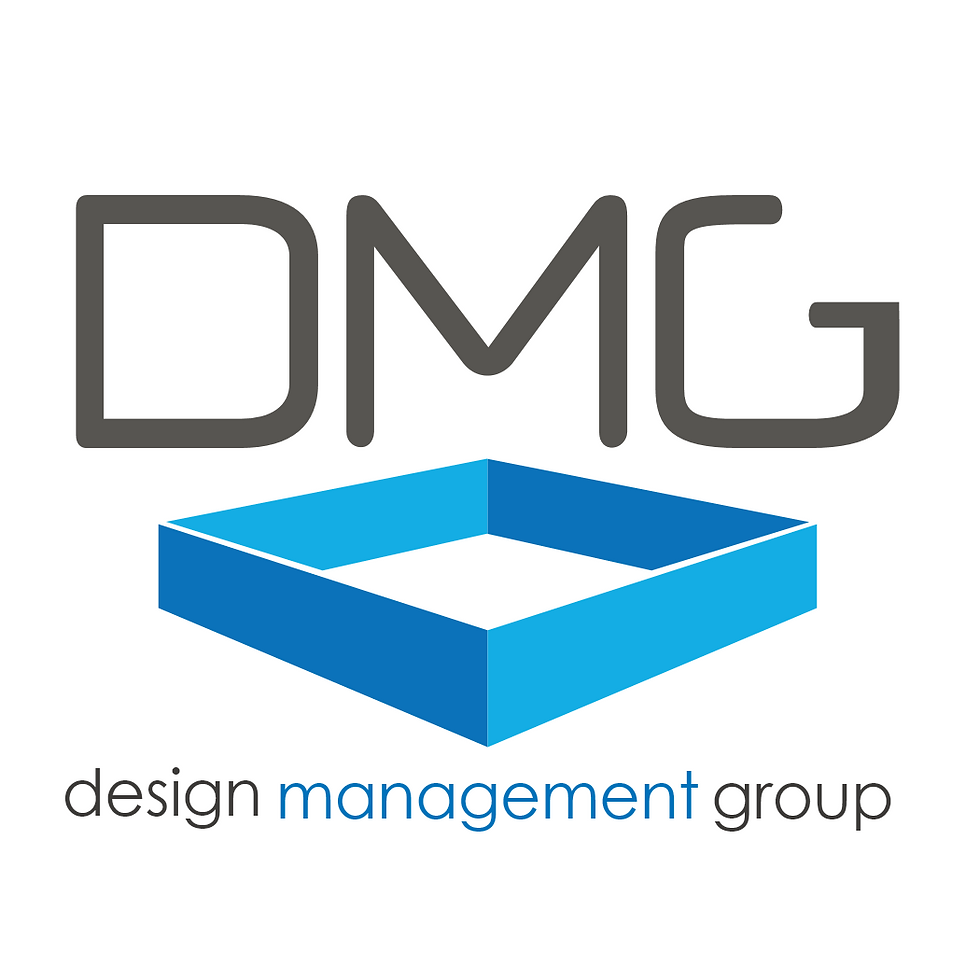